Steep Hills, road work and High Altitude
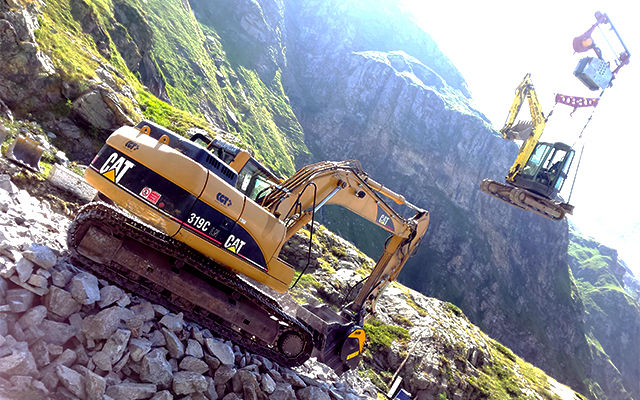
There are several challenges working on mountainous constructions sites- whether it is building or maintaining trails, fire breaks, ski slopes or clearing the roads of logs and branches. The obstacles include:
- Bringing the material up to the site is sometimes impossible if not expensive.
- The supply and the cost of transporting the material is too high.
- The nature of the job site must be preserved in order not to alter its balance.
Therefore it is necessary to find quick and easy solutions that transform these obstacles into advantages, including the economic ones. Here, are stories of those who succeeded by installing MB Crusher attachments on their heavy machinery.
- Bring the machines to their destination with difficult or non-existent access routes.
When roads are narrow and twisted, specialized transportation usually cannot pass.
This is what happened on a construction site in Friuli Venezia Giulia, Italy, where no trucks could pass through the narrow and twisted streets. The solution was simple: Attach the equipment needed to perform the job to the machinery already making its way up to the job site. This is where the MB Crusher BF120.4 jaw crusher shined: it’s attached to the excavator as it made its way up the mountain! The operator arrived at his destination and immediately started working. Without leaving the excavator’s cab, the operator crushed the rock already present on the site to create a new path.
AVOID TRANSPORTING THE NECESSARY MATERIAL TO PREPARE THE TRAILS
A lot of gravel is needed to make and maintain forest trails. So how do you get the material when transporting it to and from the valley is impractical?
By attaching the BF90.3 crusher bucket to an excavator, a Serbian company worked autonomously: crushing the rocks to the size needed to create the trails. The advantage: by not transporting the material to the valley, logistical difficulties are eliminated, saving time and money.
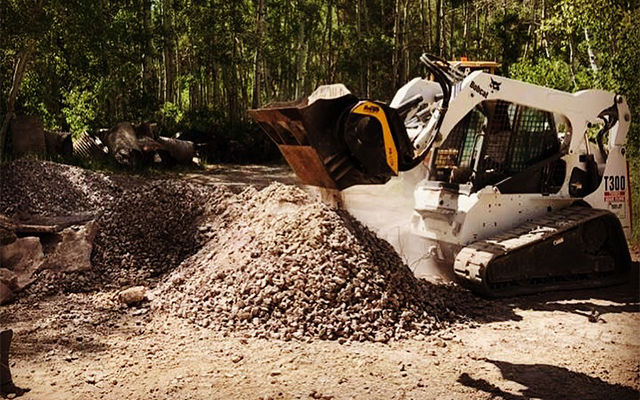
SAVING RESOURCES BY UTILIZING THE MATERIAL AVAILABLE ON THE JOB SITE AND REDUCING SOIL CONTAMINATION
There are plenty of natural rocks and river stones in the mountains.
With a skid steer equipped with an MB-L120 crusher bucket, an American company crushes them into usable sizes so that they can be immediately reused.
The company created the base material for firebreaks by using the MB crusher bucket to process and recycle granite and river rock. By using the unit, the department eliminated all material hauling costs, by using this method for future projects, they can save hundreds of dollars on transportation fees.
CONSTRUCTING SKI SLOPES
Preparing for the tourist season requires a great deal of resources to optimize facilities and locations. Mountain trails are not solely used for hiking: in the winter the snow transforms many villages into renowned ski resorts.
The slopes must be prepared well in advance. In Austria, a BF120.4 crusher bucket followed the ski slopes’ route, while crushing limestone and using it as base material.
CLEARING ROADS
Forest roads often need to be cleared of logs, branches and debris. When installed to an excavator, the MB grapples are the right units.
Everyone remembers the storm that hit Trentino Alto Adige, Italy in 2018, causing enormous damage to the forest.
Due to their ability to handle different material regardless of its shape or size, MB Crusher grapples removed tree trunks from the roads.
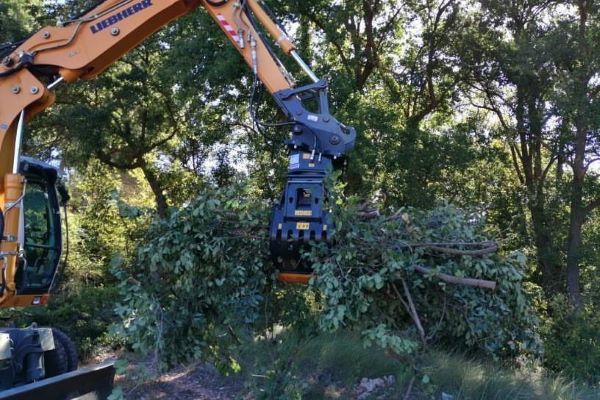
Often, mountain roads must also be cleared of vegetation and branches that grow and impede the passage. Everything is easier with MB Crusher’s grapples: just install them on any brand excavator, and if necessary, equip them with any of the various accessories and start working.
SEPARATE DIRT FROM THE STONES
Separating and managing excavated material is another critical point when constructing forest roads. An expensive solution is to use trucks to move the material up and down the mountain. With MB Crusher screening buckets, you can reach any construction site and process the excavated material directly on site.
On a construction site in Canada’s woods, creating roads that connect the forests and the residential areas created an advantage: separating the dirt from the stones using the MB-S10 screening bucket directly on site eliminated purchasing new material. The other benefit was protected the environment: by using the materials already present on site.
Applying MB Crusher machines to construction sites all over the world present an opportunity for agricultural and forestry companies that struggle with inaccessible places, high operating costs, and laws that protect the environment.
MB Crusher units:
- lets you work on the spot, wherever it is;
- has the ability to crush excavated material, select it, and make it immediately available to be reused or to be resold;
- can handle various types of materials;
- can be maintained directly on site.